For today's manufacturers, technology developments are moving at lightning speed. The introduction of robotics on production lines is advancing automation, drones are being used for warehouse transportation to achieve new efficiencies, and Internet of Things sensors are being used to constantly gather and feed data back on equipment to support ongoing maintenance and enhance performance levels.
These new technologies are being embraced by manufacturers to remain competitive - something that has become even more important as global supply chains have faced disruption from the global pandemic and manufacturers have worked hard to ensure the right health and safety measures are put in place for operating their facilities. Technology is being introduced to improve supply chain efficiencies, production techniques, inventory management and online ordering methods. However, this can place more pressure on already stretched network connectivity.
The right network services
Powering day-to-day manufacturing operations requires high bandwidth. Manufacturers need to connect hundreds of employees, customers, suppliers and partners across multiple locations and disparate geographies. Networks and infrastructure need to be able to cope effectively with these demands. For any modern enterprise, this can be a challenge, but in manufacturing it is even more nuanced.
Technology is being introduced to improve supply chain efficiencies, production techniques, inventory management and online ordering methods.
Manufacturers are becoming more reliant on the adoption of cloud, artificial intelligence, 5G and IoT applications. To keep up, it's important that they have the ability to adapt their infrastructure to support new trends and ensure they have the right network services provider in place to deliver the best results for the enterprise and its customers.
Reimagining the manufacturing life cycle
As a result of changing market demands and the expansion of technological capabilities, the whole manufacturing life cycle is being conceived anew. In the past, manufacturers sold products. If those products broke, they might offer replacements and repairs. Today's manufacturers are selling products on subscription together with ongoing maintenance services.
Technological advancements in areas such as sensors, combined with omnipresent connectivity and the rise of subscription-as-a-service models through the cloud, has changed the way that products are purchased and consumed. It offers increased possibilities for product life cycle management, allowing manufacturers to deliver products with new services attached, such as fault-monitoring and proactive maintenance and repair. Where IT used to be a support function, it's now become a value center for manufacturers and, in some instances, part of the core product that manufacturers offer.
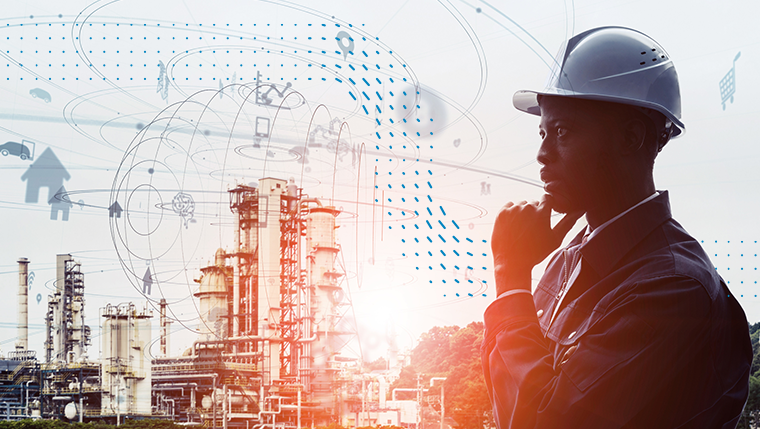
As internet-based services have developed, opportunities for increasing levels of sophistication and accompanying revenue streams are springing up all around. As a result, bandwidth requirements are exploding. Networks are also becoming more complex and difficult to manage. For example, some manufacturers need a way of communicating with the product once it's gone to the customer and providing connectivity to products on a customer's premises so they can offer regular maintenance and support services remotely.
Rethinking networks
To support new business models and reap the benefits of new technology, manufacturers need to revisit their underlying IT architecture and rethink existing networks to ensure reliable connectivity is established securely and cost-effectively for the entire product and service life cycle. Traditionally, manufacturers built their IT infrastructure capabilities in-house. Typically, a private MPLS network would connect to a supporting data center in a closed loop. Only a small set of applications would be run on this type of network design, although they might also be transmitting large design files or data volumes to facilitate production.
Now, there is a rise in manufacturers seeking to build a more connected IT environment. Many are pushing to connect to their own sites for manufacturing processes, sharing information to their partner sites, tracking the logistics of products on route and providing software updates to equipment within a customer's environment. At the same time, as manufacturing becomes more connected, there is also an explosion of data from devices at the edge of networks that are monitoring various parts of the manufacturing process. This data can be used to make the overall process more efficient and works hand in hand with automation in the factory.
Where IT used to be a support function, it’s now become a value center for manufacturers and, in some instances, part of the core product that manufacturers offer.
When thinking about the infrastructure that supports this product life cycle, there are many more areas within the supply chain that manufacturers need to connect to, monitor, and seize or cede control of. Each scenario benefits from quite different connectivity models. For example, in-house machines that don't move benefit from a fixed connection to ensure consistency in the connection. Robots or other non-static devices may use Wi-Fi or other short-range communication methods to transmit information, with 5G increasingly emerging as a strong contender for this kind of application. However, the lack of a fixed line means that there can be power issues. As enterprises rely more on wireless solutions, sufficient infrastructure needs to be in place to avoid major disruptions to the connectivity.
SD-WAN: a new connectivity model
Manufacturers need to create a coherent mesh of connectivity options. Around-the-clock system support is a growing customer expectation, so manufacturers need to be able to connect with their products to ensure functionality. Many companies have implemented private or virtual connections with their industrial robots so that they can be monitored and fixed if necessary.
In some cases, the manufacturer will need to connect to the client's corporate network. Software Defined-Wide Area Networking provides manufacturers with more agile methods to get traffic to each location and to public internet applications - it also means a broad array of access options, including fiber, cable, DSL and wireless, can be used to deliver applications in minutes on any platform.
When thinking about the infrastructure that supports this product life cycle, there are many areas within the supply chain that manufacturers need to connect to, monitor, and seize or cede control of. Each scenario benefits from quite different connectivity models.
SD-WAN allows manufacturers to use various connectivity methods for flexibility and reach. For example, it may be prohibitively expensive to build fiber out to a remote site, but there may be broadband internet availability. SD-WAN allows a connectivity solution to incorporate "lower grade" connectivity and improves the quality so enterprise applications run over the top. It may be possible to connect the site more quickly, and with two diverse lines and automatic failover so manufacturers can get comparable performance, most likely at a lower cost, and wield the two sets of requirements together.
At the same time, parts of the control plane are centralized to make management simpler. Rules and policies can be automatically distributed and implemented in seconds, lowering operational costs for IT. SD-WAN maximizes bandwidth resources at headquarters, branch or cloud sites and ensures high-quality services by intelligently leveraging multiple paths, including broadband connections. It helps identify and prioritize services so apps run smoothly.
SD-WAN maximizes bandwidth resources… and ensures high-quality services by intelligently leveraging multiple paths, including broadband connections. It helps identify and prioritize services so apps run smoothly.
Each scenario that arises could potentially benefit from a different connectivity model, so manufacturers need to understand how to create a flexible connected environment. Networks are growing and becoming more complex, but SD-WAN marries the power of the internet with greater use of software in wide area networking.
Maintaining a competitive edge
To benefit from application-aware, low-latency connectivity, manufacturers could work with a trusted provider of SD-WAN that can equip them with the agility to respond to changes in the market while meeting customer, partner, supplier and internal needs.
Through the creation of new business models, manufacturers are finding new opportunities that allow them to maintain a competitive edge and to evolve. Increasingly, software defined intelligent networks are key and provide the backbone for delivering new products and services. To offer new services, manufacturers can work with a provider with experience in their industry to ensure they identify the right network approach to balance the different demands of today's highly connected and intelligent manufacturing environment.
About GTT
GTT connects people across organizations, around the world, and to every application in the cloud. Our clients benefit from an outstanding service experience built on our core values of simplicity, speed, and agility. GTT owns and operates a global Tier 1 internet network and provides a comprehensive suite of cloud networking services. We also offer a complementary portfolio of managed services, including managed SD-WAN from leading technology vendors.
